Special Effects Sculpting Brings Copper to the Center Stage
Versatile is a word best used to describe sculptor and special effects artist, Andre Freitas. One day he might be working on a zombie for The Walking Dead television show and the next, he’s working with bronze to create a life-size dinosaur for a museum.
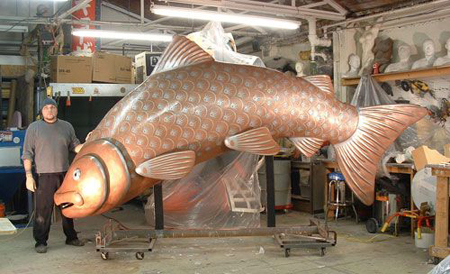
Photograph courtesy of AFX Studios.
“Every job is pretty different,” Freitas says. “I just finished working on Captain America 3 for Marvel. Now I'm working on 24: Legacy for Fox, which is a brand new reboot that will air right after the Super Bowl.”
In some cases, Freitas, owner of AFX Studios in Marietta, Georgia, might fabricate, sculpt or build in metal and then apply makeup to create the desired effect.
“We are part of the makeup department for 24: Legacy,” Freitas says. A request might be something as small as sweat on a forehead or a bruise, which is in contrast to a full-body zombie request for The Walking Dead that might take him three hours to prepare.
Freitas was first introduced to the craft as an apprentice at the Smithsonian Institution at the age of 15.
“I worked with the Office of Exhibits that builds all of the exhibits and props for the Smithsonian,” he said. “I learned about how they do their thing.”
Freitas went from learning more classical sculptural techniques to learning other, more cutting edge approaches, after a stint in Los Angeles.
“I was supposed to start college, but I went to LA to see where my work stands,” he says. “I was with a whole bunch of high-level artists who were doing it at a fast time--I got to learn all of the fast-forward techniques.”
After he was in LA for two weeks, Freitas was hired by a special effects company and that is where his professional life began. He soon delved into starting his own special effects business that would later evolve into offering a full range of special art services.
“I found a studio and had a small space to work and I was still working part-time in a hardware store,” he says. “Now I’m working in a 5,000 square foot studio.”
In 1999 Freitas began working with a unique, cold-spray metalizing system called LuminOre when he was creating a character that involved Gene Simmons of Kiss and wrestling.
“I developed ‘The Demon’ for WCW Wrestling,” he says. “We licensed their music 'God of Thunder' as part of a cross marketing deal between wrestling and Kiss. There was a resurrection chamber the character would come out of.”
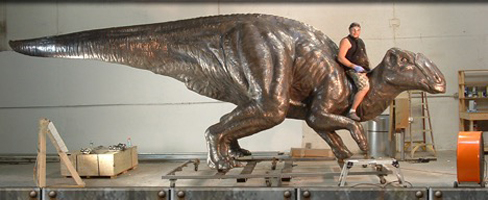
Photograph courtesy of AFX Studios.
Some artistic direction from Gene Simmons led Freitas to discover LuminOre, a product that made it possible for the dome of the Bellagio Hotel and Casino in Las Vegas to be coated in brass.
“He didn’t want silver spray paint,” Freitas says of Simmons’ input on The Demon, adding that after he received training on the LuminOre composite systems, he was able to make the character’s body armor, and the exterior of the resurrection chamber, bronze and silver with a black patina.
Freitas quickly began seeing the benefits of using LuminOre for his clients and how this system could serve as a way to cross over into commercial art projects.
“I could control this cost of metal by utilizing these types of composites,” he says. “You can control the weight and the delivery time and the price. It mimics metal, but it is just a coating — it is really thin. Real metal takes a while to have it cast.”
He discusses a project that involved creating a gigantic, copper-coated fish with aluminum details for the scales, eye and fins.
“If I’m doing a giant fish for a building, there is no way I’m using copper sheeting and aluminum,” he says, illustrating how a metal veneer that cures quickly would be the perfect solution in this case because the look can be achieved with a controlled weight scenario.
The project involving the dinosaurs for Fernbank Museum of Natural History in Georgia, was centered on bronze.
“The life-size dinosaurs are bronze coating with a black patina,” he says.
There is a good reason LuminOre is indistinguishable from solid metal, whether his project at the time dictates him using copper, bronze, aluminum or stainless steel.
“It doesn’t just look like metal — it is metal,” he says. “It contains 80 to 90 percent metal powder. It is copper going in there — it’s not a fake version. LuminOre is a composite of two materials that make a new material. You are mixing a very fine ink grade dust version into a region catalyzing.”
After applying the decorative finish, that can be added to almost any substrate, the work is not done. Just like forged metal, it can be sandblasted, sanded, polished, brushed, acid brushed, machined or given a hot patina wash.
“To get the final look, I use high-speed polishing equipment,” Freitas says. “I buff the surface of the composite. That is what makes the shine and luster.”
Freitas gets the product, that was originally designed as a furniture finish, directly from LuminOre.
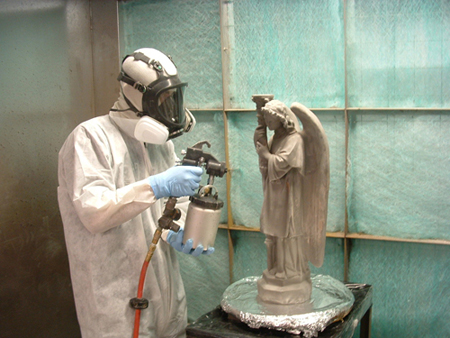
Photograph courtesy of AFX Studios.
“They are the only ones who sell it,” he says. ““There are knock-off versions, but there is nothing like the real product.”
He shares the various ways in which he approaches working with a copper LuminOre product.
“We can do patinas on it or verde greens on it,” he says. “The thing about the copper products is they can take the same patinas as metals would.”
In the case of a project for Victoria’s Secret, a client who asked for rose-colored, gold mannequins, Freitas created the color by mixing bronze and aluminum. He discusses how LuminOre makes these metal combinations possible to create the desired effect.
“You are mixing them to make it because the matrix is cold and you aren’t heating the metal up,” he says. “Both have different melting temperatures and would never work that way.”
At the current time, the majority of clients that use LuminOre are churches.
“I have been working with churches for years doing religious figures,” he says. “I think when it comes down to churches, they don’t have as much money to spend and they are looking to get the look of metal without having to pay for it.”
Regardless of the client, he discusses the various factors involved with the way he prices his LuminOre projects on a square footage basis.
“If you had a patina piece, it would be cheaper than if you have to sand and polish everything,” he says. “If it had to look like an Oscar that is mirror reflective, that would be the most expensive,” he says.
He views LuminOre as just another one of his mediums to add into the mix of his offerings.
“I never thought I’d be able to paint metal before,” says Freitas. “It’s something I never imagined.”
Resources:
Also in this Issue:
- Special Effects Sculpting Brings Copper to the Center Stage
- Copper Kingdom: Old World Inspired Copper Gaming Pieces
- Invigorating Life Size Bronzes with Classic Realism
- East Coast Tinning: Copperware’s Resilience in Restoration
- Bronze and Copper Hippo Ballerina Installed at NYC’s Lincoln Center