Return to Glory
Copper Adds Crowning Touch to Plaza Hotel Restoration
When it was announced that New York City's famed Plaza Hotel would close its doors forever, travelers from around the globe mourned the passing of an era.
Built in 1907 and situated like a cornerstone at the southeast tip of Central Park, facing the posh boutiques along Fifth Avenue, the Plaza had been the hotel destination of choice for dignitaries, celebrities and well-heeled visitors for close to 100 years.
But a century of weather and wear had taken its toll. To preserve the building's landmark status, and A-list reputation, new owners decided to fund a top-to-bottom restoration and reopen the Plaza as a luxury apartment complex. The threeyear project, costing nearly $400 million, will be completed by the end of this year. It includes new retail shops on the ground floor and 182 apartments and condominiums overlooking Central Park, including 14 penthouses nestled into the reconstructed roofline.
Some parts of the building were beyond restoration and needed replacement. Even the handwrought copper that crowned the building's French chateau-style roof had succumbed to the accelerating effects of acid rain, pigeon droppings and vehicle air pollution in heavily trafficked midtown Manhattan.
"In the condition that the roof was in, you could see daylight through the metal," says Cameron Forbes, vice president of Heather and Little, a Canadian company subcontracted to handle the ornamental copper fabrication. This part of the restoration alone cost $2 million. The work began in 2004 and was completed earlier this year.
Nicholson and Galloway, a Glen Head, New York, firm that specializes in sheet metal restoration, did the actual copper installation. The project involved restoring and building new dormers, as well as fashioning continuous roll ridges, hip caps, flashings, finials, ornamental band work and wall cladding. Copper flat and standing seam portions of the roof also had to be reconstructed. A custom-order green clay ceramic Ludowici tile, installed by Eagle One Roofing of Manhattan, was used for the new primary roof covering. Eagle One also did copper work for this project.
Six full-size mock-ups of the copper roof elements were constructed to ensure the designs would be both waterproof and structurally sound before production began. Components that could not be fabricated onsite were made in Canada by Heather and Little.
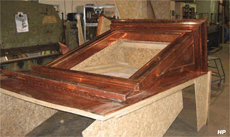
High-resolution version of this photo.
According to Forbes, a combination of 20- and 24-ounce sheet copper, provided by Revere Copper Products of Rome, New York, was used to rebuild the roof components and the dormers, which stand about 12 feet high and weigh close to 1,000 pounds apiece. Once completed, the dormers were shipped in sections, then reassembled in place on the roof's east, south and west elevations.
"We had some of the original ornamental pieces shipped to our shop so that we could replicate them," Forbes explains. "When they were done, they appeared exactly as the original ones. It's really interesting to see how well-done the craftsmanship was 100 years ago, especially with them not having the modern equipment we have today."
While Heather and Little has restored many landmark copper structures, the Plaza project was special because of its iconic place in history, Forbes says. "Just for the simple fact that the 'who's who' of movies and celebrities have been through there. It's a beautiful building. The architecture is just great."
Also in this Issue:
- Going by the Book
- Greening Fire Sprinkler Systems with Copper
- What Would Al Gore Choose?
- Copper's Design Potential Highlights Architectural Seminars
- Return to Glory