ARI and CDA Sponsor Research on Copper Joining Techniques with Future Refrigerants
Copper Applications in Plumbing
Note: This article summarizes the results of a research project, sponsored by the Air-Conditioning and Refrigeration Institute and Copper Development Association (CDA). An expanded summary can be found on ARI's homepage ( http://www.ari.org).
Introduction
Poor quality braze joints in air-conditioning and refrigeration systems and their components are estimated to cost the industry $30 million to $90 million per year in refrigerant leaks and required rework. These costs are incurred as a result of tubing and fitting defects, imperfect braze joints made in factories by both automated furnaces and human braze operators, and as a result of field failures from poor installation, handling damage, and cyclic fatigue stresses.
This article details the results of a research project undertaken at Amalgamatd Technologies Inc. (ATI) to ascertain whether current brazing techniques and methodologies for joining copper tubes are adequate for the alternative refrigerants proposed for future usage. ATI's final report indicate that there are three key criteria for obtaining full integrity within a brazed joint:
- full seating of the unexpanded mate portion of the tube (inside tube) into the female swaged socket formed by the expanded tube (see Figure 1),
- full penetration of the braze material into the female swaged socket,
- and a good fillet radius on the outside of the brazed "overlap."
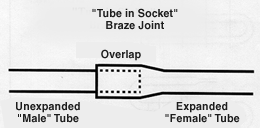
Methodology
Five facilities of four major manufacturers were visited to identify representative tubing configurations and braze materials for incorporation into the test. All manufacturers visited were found to use similar brazing technology. Similar brazing difficulties were seen at each plant. Inconsistent tube length beyond the endsheets led to overexpanding and cracking of the tubing through the joint region. Various amounts of oil residue from tube forming operations contaminated the braze joints, and led to heavy smoke and poor braze quality. These and other difficulties resulted in rework and additional expense for the manufacturers.
As a result of the visits to the manufacturers, three brazing materials and four tube types were selected for testing. Both 5/16" (8 mm) and 3/8" (9.5 mm) tubes were tested, each with and without fins.
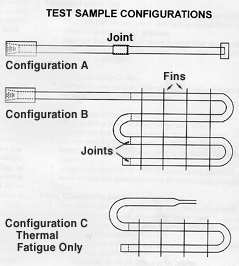
The four types of tubing were configured into three test sample types, depending on the test procedure to which they were subjected. These three types of test samples are shown in Figure 2. As can be seen, each sample contains at least one "telescoping" joint, where one tube is expanded to form a female socket, to allow an unexpanded tube to slip inside and form an overlapping joint.
The intent of the work was to ascertain what parameters affect the integrity of brazed joints in copper tubes. In equipment applications, sound joints are considered those that do not leak or develop leaks during normal operation. For the accelerated stress testing performed in this effort, tube/joint strength and endurance were utilized as indicators of joint soundness. Four different test procedures were performed in this evaluation: static burst pressure, vibration cyclic fatigue life, thermal cyclic fatigue life, and pressure cyclic fatigue life.
Static Burst Testing
In hydraulic tests, all three braze alloys proved to be stronger than the tubing, as no samples failed because of filler metal separation within the braze joint. Samples that were well brazed and had no tubing defects or mechanical damage failed at the highest pressure levels, very close to the theoretical burst strength of the tube itself.
However, most samples failed at reduced pressure below the theoretical burst strength. There were two distinct categories of these reduced pressure failures:
- Mechanical imperfections: Included tube wall thickness variation, tube surface damage from hand expansion operations, and points where the tubing is pinched against the steel end sheet.
- Incomplete filler penetration: Partial penetration joints have reduced burst strength and usually fail within the telescoping joint regions. The step of expanding the tubing to make the female socket stretches and thins the tubing wall. In addition, the tubing is fully softened by brazing heat. For maximum burst strength, there must be full filler penetration to prevent the thinned wall of the outside tube from being exposed to internal pressure.
Poor braze filler penetration is largely due to the difficulty of achieving even, uniform heating with a manually applied gas flame. The report notes that excessive joint overlap hinders full braze penetration, and offers no strength advantages.
Vibration Cyclic Fatigue Testing
The most significant result of the vibration testing was demonstrated by the 3/8" (9.5 mm) diameter tubes which-were tested for one hour with alloy BCuP-6. Because of filler metal characteristics and braze technique, each of these samples had virtually no fillet at the edge of the brazed joint. The lack of fillets caused a stress concentration at the base of the joints, which resulted in premature cracking and a significantly reduced group average lifespan. Filler metals with high silver content are highly fluid outside of a capillary space, and naturally leave only very small fillets. Specific attention is needed from a brazing operator to build up a proper fillet with the higher-silver braze alloys.
The primary conclusion from vibration fatigue testing is that vibration survival requires a sound joint with full penetration and a proper fillet.
Thermal Cyclic Fatigue Testing
Thermal fatigue was explored bv an apparatus that exposed pressurized tubing samples on a rotating wheel to a temperature range of 40F to 270F (4C to 132C). Samples were heated by natural gas burners, then quenched in a trough of water cooled by refrigeration. Tests were performed on 5/16" (8 mm) Configuration C samples only.
For the majority of the samples, there was no indication after 62,000 cycles that any kind of failure was imminent. The primary conclusion from thermal cyclic fatigue testing is that normal temperature cycling of a refrigeration coil in operation is not detrimental to the coil itself.
Pressure Cyclic Fatigue Testing
This test simulated pressure cycling effects of refrigeration system operation. Testing was limited to 5/16" (8 mm) and 3/8" (9.5 mm) Configuration B samples only. Samples were rapidly pressurized and depressurized until failure. The cyclic fatigue test procedures were performed at multiple cyclic stress levels. The high stress, short duration testing at one-minute and one hour life spans resulted in failures similar to static burst testing, as almost every sample failed in a braze joint. Most samples would fail at score marks in the joint tubing, or at a poor penetration braze joint. [Note: score marks are mechanical deficiencies that are generally not incurred in production heat exchangers. However, some of the tubes in this experiment were found to have score marks produced during hand expansion operations.]
The 24-hour life span group provided the most interesting data. The lower cyclic stress resulted in a sudden and dramatic shift in failure mode. Instead of failing on or near the braze joints, the majority of the 24-hour group samples of both tube sizes failed in the hairpin bends of the coils.
The primary conclusion from the pressure cyclic fatigue testing is that maximum working strength requires full penetration braze joints, and elimination of score marks and other mechanical imperfections.
Conclusions
Conventional brazing technology is capable of achieving high quality joints. Today's gas heating methodology and the braze alloys tested are capable of good performance. However, reaching the full potential of today's technology may require some factories to improve current application. It is suggested that tube and coil forming operations be performed more carefully, and that existing braze technology be implemented more effectively.
This study identified that full penetration of the brazed joint was essential to optimum performance. Consistent, full penetration brazing is difficult to do with a manual torch, and is hindered by excessive joint overlap. Generous fillets at the outside of telescoping brazed joints are necessary for vibrational fatigue resistance. In the test, the non-silver-content braze alloys performed as well as the higher-silver content braze alloys in achieving full penetration and proper fillet shape (with the exception of BCuP-6 for fillet shape). Mechanical damage and imperfections from coil forming, tube manufacturing, heat exchanger construction or handling operations negatively influence burst strength and endurance.
It is concluded that manufacturing quality and service life will be enhanced from improvements in the heating process to provide better uniformity and temperature control, improvements in joint design, and improvements in tube and coil forming operations.
To help answer questions in these areas, a continuation effort is underway (results expected first quarter 1998). In this continuation, an alternate braze technology (induction heating) will be utilized to ascertain the benefit of uniform heating on braze penetration into the joint, and different overlap ratios and female cup profiles will be evaluated to determine their impact on braze penetration ability and joint integrity.
ATI's Observations
Static Burst Test
- Braze filler strength and hardness have little to do with the strength of a brazed joint.
- Burst strength is most influenced by the effectiveness of braze filler penetration.
- Burst strength of one sample type was influenced by mechanical damage. Failure occurred on score marks at reduced pressure regardless of braze quality, braze alloy, or location of the thin side of the tubing wall.
- Penetration, braze quality, and filler characteristics are very important.
Vibration Fatigue Test
- Joints with poor penetration can fail rapidly from cracking within the braze filler material. Hence, joints that look good and hold pressure can fail from vibration in transport or operation.
- Improper braze fillets will cause failures from stress concentrations.
- If the proper fillet radii are formed, higher silver content brazing alloys do not appear to be superior.
Thermal Cyclic Fatigue Test
- Normal temperature operation of a refrigerant coil is not detrimental to the coil - burst strength actually increased.
Pressure Cycling Fatigue Test
- No correlation between braze alloys and failures.
- One-minute and one-hour samples failed on the braze joints.
- 24-hour samples failed primarily in the hairpin bends. (ATT theory: Tubing was initially too hard and subsequent work hardening induced shift in failure locations.)
- At cyclic pressures of 75 - 80% of burst strength, the characteristics of the tubing itself became the dominant factor for pressure cyclic endurance.
Other Observations and Recommendations
- Very little difference between the three braze alloys used.
- The overlap region of telescoping joints needs to be reduced to one tube diameter or less. Less heating demand, less filler quantity, better ability to achieve full braze penetration.
- Need to prevent overheating of joints (reduces filler fluidity).
- Better joint integrity arises by:
-
- eliminating all oil on tubing to be brazed,
- tightening tube concentricity,
- reducing unused overlap on return bends,
- preventing mechanical damage from tooling,
- eliminating saw chips and other debris,
- controlling tube lengths to eliminate tube splits during swaging and flaring operations.
This article is reprinted with permission from Koldfax, the monthly newsletter of the Air-Conditioning and Refrigeration Institute (ARI).
Also in this Issue:
- New Copper Alloys: Revised and Reactivated Alloy Compositions
- New Copper Alloys: Compositions of New Copper Alloys
- New Copper Alloys
- ARI and CDA Sponsor Research on Copper Joining Techniques with Future Refrigerants
- The Butte Copper Mines
- Paul Revere - Copper Industry Pioneer
- The History of Brass Making in the Naugatuck Valley
- Environmentally Friendly Permanent Mold Casting