Copper: Technology & Standards
Copper Applications in Plumbing
Innovative Processes
Mining and Ore Handling
The early U.S. copper industry, located primarily in the American West (Arizona, Utah, New Mexico, Montana, and Alaska) was restricted to mining very rich copper-containing minerals. The introduction of the flotation process in the late nineteenth century permitted the extraction of copper and other metals (including gold and silver) from low-grade porphyry ores. Figure 1 illustrates the ore haulage from an early mine using small rail cars, whereas today's ore handling employs 200- to 300-ton trucks and gigantic shovels ( Figure 2). In the mid-1980s, one mine introduced a gigantic, highly engineered conveyor system ( Figure 3).
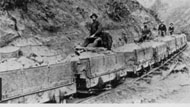
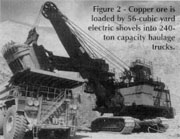
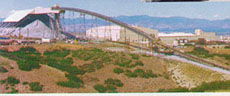
Flash Smelting
Improved bath and smelting technologies have successfully increased smelter productivity and efficiency, while enabling compliance with increasingly stringent environmental restrictions.
Electrorefining
In the past decade, starting sheets made of stainless steel or titanium have been substituted for the traditional copper in a number of refineries employing the electrolytic refining process. Deposited copper is separated from the stainless steel or titanium starting sheet by use of a guillotine and/or by flexing with an air blast. Very significant labor-cost reductions have also been achieved because of the introduction of automated handling of anodes and cathodes in the tank house.
Solvent Extraction
Traditional sulfide ore grades require conventional milling, smelting, and refining. Solvent extraction permits the processing of low-grade oxide ores at much lower cost.
In the first stage (leaching), acidic water (dilute sulfuric acid) is distributed over 60-foot high ore pile layers by wabblers, drip irrigation devices or sprinklers (rain birds), and allowed to percolate through the pile dissolving copper as it penetrates. The copper-laden water or "pregnant leach solution" exits from the bottom of the ore pile or dump and flows to a collection pond from which it is pumped to the solvent extraction plant. The pregnant leach solution is then mixed vigorously with a kerosene-based solvent containing an organic chemical specifically designed to extract copper. The copper-laden organic material, loaded organic, is next mixed with a copper-bearing sulfuric acid solution known as the electrolyte or the aqueous solution. In the mixing and settling stage, the copper is transferred from the organic to the aqueous solution, filtered and then pumped to the electrowinning tank house.
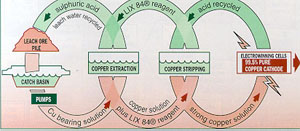
Electrowinning
In the electrowinning stage, copper from the rich electrolyte is deposited for seven days onto either copper cathode starting sheets or stainless steel or titanium mother blanks as in the electrorefining process. The anode is made of lead In 10 days, each copper starter sheet grows from its original weight of about 1.7 lbs (7.7 kg) to a cathode of virtually pure copper weighing about 200 lbs (90.8 kg). The electrowon copper cathode produced meets the requirements of ASTM B115, Specification for Electrolytic Cathode Copper, which, along with electrorefined copper, is traded on the world's metal exchanges.
Flow of Copper
The flow of copper from mine or recycled metal scrap pile to end markets is illustrated in Annual Data PDF. In brass mill operations, alloying metals such as zinc, lead, tin and nickel are introduced which are covered by companion ASTM specifications under the jurisdiction of Committee B-2.
Continuous Casting
Probably the single most important innovation in the copper industry in the past generation, from a commercial and technological standpoint, has been the introduction of continuous wire rod technology. Rod produced by this method is the basic feed material for the electrical wire and cable industries.
Changes in production techniques came very fast, leading to almost worldwide replacement of the traditional 250-lb (113.5-kg) wire bar with the continuous wire rod product. Continuous casting allows coils to weigh up to 10,000-lb (4,540-kg). Before the size of a coil was limited by the mass of the 250-lb wire bar it was created from. Coil size is limited only by the capacity of the handling equipment. Copper receipts by wire rod mills as cathode, which is essentially equal to that portion continuously cast have grown from under 2.5 million pounds in 1987 to almost 3.5 million pounds in 1996. Continuously cast wire rod meets the requirements of ASTM B49, Specification for Hot Rolled Copper Redraw Rod for Electrical Purposes.
Continuous or semi-continuous casting is also used to produce cast cake for conversion into plate, sheet, and strip, as well as for continuously cast logs which are sawn into billets and are the intermediate products for conversion into pipe, tube, and rod.
Innovative Products
Increasing numbers of fabricating companies have converted their multi-alloy multi-product lines into single product lines with a limited number of alloys. Examples include tube, strip, and rod products, the manufacture of which was encouraged by processing improvements.
Analytical Control
Refineries and brass mills have benefited from the introduction of analytical instrumentation that permits very rapid determination of the chemical composition of the molten metal in the holding furnace and provides impurity control prior to casting.
Seamless Tube
Advances in the manufacture of seamless copper tube for plumbing, refrigeration, medical gas, natural gas and liquefied petroleum gas have helped make copper the overwhelming material of choice in quality residential, commercial, and industrial building construction.
Historically, seamless copper tube production began by converting a solid billet to a hollow shell by a piercing process. Extruded shells of much thinner wall thickness were introduced to the market in the 1950s when large extrusion presses became available that could provide the necessary higher extrusion ratio. Further, these shells were suitable for cold drawing on bull blocks and spinner blocks in significantly higher unit weights than was formerly possible on draw benches.
A major development in bull block design was the extensive use of spinner or continuous blocks for tube drawing, a principle adopted from the wire industry. High-speed combination machines clean, straighten, test, mark and cut the tube to specified lengths before discharging the product to bundling equipment for straight lengths or recoiling it for subsequent bright annealing of the stock for users of soft coils.
The irregular wall thickness tolerances that existed in ASTM B88, Specification for Seamless Copper Water Tube, were converted to a uniform �10% several years ago. They are currently being restudied based on an in-depth engineering evaluation.
Seamless tube intended for air-conditioning applications is being increasingly made by the Schumag process, which involves a straight draw with a carbide floating plug. This process provides improved wall thickness control with superior concentricity.
Tube for medical and natural or LP gas applications requires superior inside surface cleanness. This requirement is accommodated by immersing the tube in tanks containing suitable chemical cleaners, and then testing the tubular product per the procedures contained in Specifications B819, for Seamless Copper Tube for Medical Gas Systems or B837, for Seamless Copper Tube for Natural Gas and Liquefied Petroleum (LP) Gas Fuel Distribution Systems.
Welded Tube
In the mid-1960s, welded copper and copper alloy tube produced from strip without the use of a filler metal became commercial. Strip from payout reels is formed in successive stages to the round tubular shape, and is then welded by one of several optional methods. The dominant specifications are ASTM B447, Welded Copper Tube and ASTM B543, Welded Copper and Copper Alloy Heat Exchanger Tube. Major advantages include the opportunity to use excess brass mill strip capacity, the production of selected tube lengths without metal wastage, the production of long level wound coils suitable for use in refrigeration and air conditioning, and other uses as oil and gasoline lines. Tighter wall thickness tolerances are another advantage.
In household application, the use of welded yellow brass (C26000) tube shows slow but steady growth in plumbing, drainage (sink traps) and architectural applications as well as products such as (head/footboards and lamp poles).
Enhanced Tube Surfaces
The revised specification ASTM B359, Specification for Copper and Copper Alloy Seamless Condenser and Heat Exchanger Tubes with Integral Fins, is specified for highly engineered surface condensers, evaporators and other specialized air-conditioning equipment. A companion specification using welded tube blanks is also under development. Such tube has had its external or internal surfaces, or both, modified by a cold forming process to produce an integral enhanced surface for improved heat transfer associated with nucleate boiling. Prompting this effort has been the withdrawal from worldwide production of certain ozone layer destroying refrigerants such as R11 and R12 according to the 1995 Montreal Protocol. The replacement refrigerants R134a and R123, while not exhibiting this destructive behavior, are not as thermodynamically efficient; hence the need for tube with superior heat transfer characteristics.
Plate, Sheet and Strip
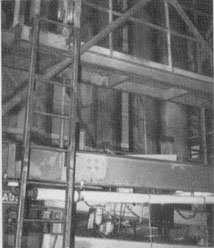
These products start as direct chill cast cake whose size has increased from 7,000 lbs to 55,000 lbs (3,200 kg to 25,000 kg). Because of the larger coil sizes being produced, improved metal quality and production efficiencies are achieved. Precision slitting for strip width control and freedom from edge burrs along with other improvements are now standard. A strip annealing furnace, which provides superior grain size control, reduces labor requirements, and conserves factory floor space over conventional bell annealing furnaces, has been introduced into production operations.
Bus Bar
Rolling has largely replaced drawing procedures in domestic fabricating mills leading to improved product quality and production efficiency.
Not well known is a contribution made by the U.S. copper industry to the Manhattan Project during World War II. There was an urgent need for copper bus bars for the Uranium 235 extraction facility in Oak Ridge, Tenn. Because all available copper was being directed to the conventional war effort, a substitute material with comparable electrical conductivity was needed. (The electrical conductivity of silver is rated at 104% IACS, whereas copper is rated at 100% IACS, which made it a suitable substitute.)
Some 700 million troy ounces of pure silver (equivalent to today's ASTM B413 (Specification for Refined Silver) Grade 99.95 (UNS P07015)) were borrowed from the U.S. Treasury and shipped to the U.S. Metals Refining Company (USMR) in Carteret, N.J., remelted and cast into pure silver wire bars. The wire bars were then shipped to Phelps Dodge's Elizabeth, N.J., facility for rolling into bus bars (equivalent to today's ASTM Specification B187, for Copper Bar, Bus Bar, Rod and Shapes). In the late 1970s, the silver bus bars were removed from service, returned to USMR for melting, refining, and casting as 1,000-troy ounce ingots and returned to the Treasury.
Rod
The brass rod and bar industry, which produced almost 1.1 billion pounds (500 million kg) in 1996, has introduced semi-continuous castings of larger-size quality extrusion billets and has increased the capacity of its extrusion presses from 2,000 tons to 6,600 tons (1,814,000 kg to 5,986,200 kg).
This has led to elimination of extrusion defects and to larger coil sizes at vastly improved production rates that, when combined with improved straightening equipment, has resulted in a superior product for feeding multiple spindle screw machines.
Wire
Natural diamonds for drawing dies have largely been supplanted by polycrystalline artificial diamonds. Enhanced die design has led to improved surface conditions by significantly reducing surface oxides, while achieving superior mechanical properties.
Multi-wire drawing machines are now common along with superior insulating varnishes, permitting higher-temperature electrical conductor applications. In the case of magnet wire, motor sizes can be shrunk because of this elevated temperature capability.
Major Markets
Numerous applications exist for various copper alloys where their unique properties make them the material of choice. The following examples highlight major market uses.
Building Wire and Other Wire Products
Building wire is the largest market for copper in the United States. In 1997, copper usage was approximately 1,400 million lbs. (636 million kg), accounting for 16.9% of all copper metal shipped. The number two market in the wire family for copper is magnet wire, amounting to 700 million lbs (318 million kg). It is used in motors, generators, and transformers, and accounts for 18% of all copper wire mill products shipped. A smaller but still important area for copper is in power cable.
Automotive Electrical
Automotive wire and cable (except magnet wire) represents 300 million lbs (136 million kg) of shipment in 1997. The electrical system of the modern passenger vehicle is a complex maze of components, wiring and terminals. It reflects the increased use of power, lighting, control devices, entertainment features, and all other conveniences expected in the modern automobile and light truck.
Copper alloys selected for non-elevated temperature applications in vehicles include: beryllium-copper (C17200) strip, produced to ASTM B194, Specification for Copper-Beryllium Alloy Plate Sheet Strip and Its High Temperature Properties; yellow brass (C2 000), produced to ASTM Specification B36, Brass Plate, Sheet, Strip, and Rolled Alloys; and tin brass (C42200/C42500), produced to ASTM B591, Specification for Copper-Zinc-Tin Alloy Plate, Sheet, Strip, and Rolled Bar. Lighting contacts are made from the phosphor bronze alloys (C51000/C52100) in accordance with ASTM Specification B103, for Phosphor Bronze Plate, Sheet, Strip, and Rolled Bar.
Several new alloys have also been developed for elevated temperature applications such as in catalytic converters.
Computers
Recently alloy C66300 (nominally 86% copper, 2.2% tin, 2% iron + cobalt, remainder zinc) has found successful application as a lead frame connector for Pentium chips in the computer industry.
Plumbing
Copper plumbing tube continues to be a major factor in building construction in the three wall thickness schedules produced. In 1997, copper usage for plumbing was 652 million lbs. (296 million kg) accounting for 18.9% of all copper metal shipped in the United States. The dominant specification is B88, Seamless Copper Water Tube.
Air Conditioning and Refrigeration
The outstanding corrosion resistant and heat transfer properties of copper has contributed to the enormous growth of the air conditioning market particularly in the Sun Belt states. Population and industrial growth can be directly linked to the expansion of air conditioning made possible, in large measure, by the use of copper in its equipment (Figure 19). Visualize the movement of persons from air-conditioned homes to cars to shopping malIs to manufacturing facilities. The dominant specification is B280, Seamless Copper Tube for Air Conditioning and Refrigeration Field Service.
Automotive Radiators
The automotive radiator is the single largest market for brass strip in the United States, even though its share of the market has been eroded by aluminum. ASTM B569, Specification for Brass Strip in Narrow Widths and Light Gage for Heat Exchanger Tubing, was created to accommodate the product requirements for the manufacture of thin-walled tubes for water passages in heat exchangers for internal combustion engines and other closed-system heat sources.
Coinage
Over the past decade and a half, the Government of Canada has withdrawn its one- and two-dollar paper currency bills and substituted copper-based metal coins, commonly referred to as "Loonies" (so named for the symbol of the loon on the back of the one-dollar coin) and "Toonies".
In February 1998, the U.S. Coin Coalition met with representatives of the U.S. Department of the Treasury and the U.S. Mint to review technical aspects of a new dollar coin. The coin, expected to be a copper alloy, is scheduled for minting in the year 2000 as part of Public Law 105-124 (December 1, 1997).
The law specifies that the new coin shall have the same diameter as the current Susan B. Anthony coin, that it be golden in color with a discernable edge, and that the coin and its components (strip and blanks) be manufactured within the United States. Design and security requirements, which refer to a unique electromagnetic signature for measurement by automatic coin reading machines, are also critical. The U.S. Mint is seriously testing two clad metal systems-a Golden Nordic coin (similar to the Swedish kronor) and a modified British pound. Public and commercial acceptance of the new dollar coin will dictate whether the dollar note will be withdrawn.
Copper Roofing
For the past decade and more, there has been steady growth in copper sheet and strip for copper roofing in the United States and Canada. Specification ASTM B370, Copper Sheet and Strip for Building Construction, in its multiple thicknesses or gages, is the basis for specification and purchase. Fueling this healthy market are the competitive availability of the metal plus the confidence in copper.
Just recently adopted has been ASTM B882, Specification for Prepatinated Copper for Architectural Applications. Such a product has long been wanted by architects and engineers who did not want to wait years for the copper roof or building fascia to develop the prized green color.
Low-Lead and Lead-Free Wrought and Cast Copper Alloys
Concern about the health effects of lead leached into water prompted the reconsideration of existing alloys and the development of new alloys for potable water application. Pressure tightness for castings and superior machinability for both wrought and cast components provided by the lead addition were mandatory requirements. Wrought and cast lead-free bismuth containing alloys met these properties including the health requirements of ANSI/NSF 61, Drinking Water System Components-Health Effects. An acidified sodium acetate wash has been demonstrated to remove smeared lead following machining.
Concern has been expressed by some segments of the industry for mixed scrap in which trace amounts of bismuth could lead to hot shortness of the metal during processing. Procedures for rigid control and segregation of recycled scrap are under study by the Institute of Scrap Recycling Industries (ISRI) and the Brass and Bronze Ingot Manufacturers (BBIM).
Household Products
In household products, copper metals are selected because of their superior combination of appearance, quality, image, design factors, physical and mechanical properties, and long service life. Electrical lighting fixtures is the major household product category along with fireplace equipment.
Service Activities
Susceptibility of Copper Materials to Stress Corrosion Cracking
The traditional method for determining a copper material's sensitivity to stress corrosion cracking has always been the mercurous nitrate test (ASTM B154). In response to the request from the ASME Boiler and Pressure Vessel Code and the U.S. Coast Guard, Committee B-5 undertook the conversion of ISO 6957 Copper Alloys-Ammonia Test for Stress Corrosion Resistance, to ASTM format. This was prompted by their concern for test solution and specimen disposal. ASTM B858M, Test Method for Determination of Susceptibility to Stress Corrosion Cracking in Copper Alloys Using an Ammonia Vapor, is now official. The test method simulates service conditions under which stress corrosion cracking may occur and overcomes the shortcomings of the mercurous nitrate test.
The Future
The world's economy is rapidly becoming global. With the approach of the 21st century, third world countries are establishing telecommunications links, becoming greater consumers of electricity, and they are constructing homes, factories, and commercial buildings. Copper will be required to meet these needs. Copper has been used as an engineering material for almost 10,000 years, and its services to mankind are myriad. It is impossible to envision a world without it.
Art Cohen
Arthur Cohen, consultant to the Copper Development Association Inc. (CDA), recently retired from his position as manager of Standards and Safety Engineering with CDA. The 1996 chairman of the ASTM Board, Cohen has received the ASTM Award of Merit (1977), the Committee B-5 Certificate of Appreciation (1981), the Copper Club/Committee B-5 Award (1983) and the SES Leo B. Moore Medal (1992), among many other awards. He has authored over 50 articles and several chapters for technical handbooks.
ASTM Committee B-5 salutes the Society's centennial. The committee was formed in 1929 as an outgrowth of Committee B-2 on Nonferrous Metals and Alloys. Its mission was to create copper standards in cooperation with the Copper and Brass Research Association and its successor, the Copper Development Association Inc.
This seven-decade partnership with ASTM has established worldwide-accepted standards that reflect the great advances and technological changes which have occurred with the industry. Canada has also completely embraced ASTM copper standards.
There are many breakthrough areas where ASTM standardized products and methods have been introduced.
Also in this Issue:
- Adjusting to Dramatic Changes Occurring in the Interconnect Market - What’s Next for the World of Interconnects?
- The Metal of Civilization Standards B115 and B49
- Copper Motor Rotor Research Update
- Copper: Technology & Standards
- New Copper Alloys - Summer 1998