Copper at the Cutting Edge: The Copper Vapor Laser
Copper Applications in Innovative Technology
- Laser
- Copper Vapor Laser
- Kinetic Enhancement of the Copper Vapor Laser
- Micromachining with the Copper Vapor Laser
- Microdrilling
- Microcutting and Milling
- Other Applications of the Copper Vapor Laser
- Future Prospects for the Copper Vapor Laser
The Copper Vapor Laser, already the natural choice for precision micromachining, has just gotten better.
Although the copper vapor laser (CVL) has been known for more than 15 years, it is a relative newcomer to the family of engineering lasers, and it is thus less widely used than carbon dioxide, Nd-YAG and excimer lasers. That may soon change. The copper laser already has many diverse applications, and because of its inherent beam characteristics, it has recently established itself as the natural choice for high precision micromachining of features down to 1 µm (40 millionths of an inch.)
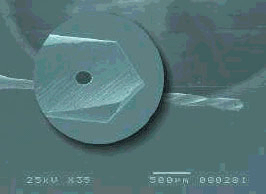
The laser's micromachining capabilities are illustrated in this photo of a drill bit, which has the diameter of a human hair (160 µm). A CVL beam machined a 20-mm hole in the tip of the drill. The hole is as drilled; no post processing has been carried out, attesting to the level of quality possible with CVL micromachining.
Remarkable as the copper-based laser is, it has recently been improved. Based on research and development work at Macquarie University in Australia, Oxford Lasers has introduced kinetic enhancement to CVLs they manufacture. This feature dramatically improves the power, brightness and pulse repetition frequency of the lasers, enabling higher machining speeds at lower cost.
Back to TopLaser
First, a bit of physics. LASER is an acronym for Light Amplification by the Stimulated Emission of Radiation. The emission of radiation is stimulated when atoms are excited to an energy state above their ground state, and are then permitted to decay back to that ground state. More lasing atoms have to be excited to the energy level above the ground state to produce a population inversion with respect to the number of atoms in an intermediate energy level. All the excited atoms are stimulated to decay coherently to the intermediate energy level, resulting in intense electromagnetic radiation at a wavelength corresponding to the energy gap between the excited and intermediate states. The electron transitions for the copper vapor laser are illustrated in Figure 2.
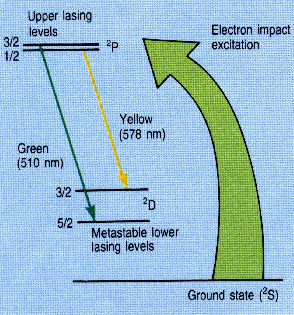
The stimulated emission gives a laser beam special properties that uniquely distinguishes it from the light generated by conventional sources:
- It consists of only a few discrete wavelengths;
- It is coherent, i.e. the light waves are all in phase;
- It is unidirectional; and
- It has low divergence
These features enable the beam to be focused to a very small and intensely powerful spot, and there is rapid energy transfer to a material that interacts with the beam. The energy is sufficient to vaporize a portion of the target, "machining" it as it does so. The wavelength of the laser light depends on the lasing material, which is usually either a solid or a gas. The carbon dioxide gas laser emits infrared light at a wavelength of 10.6 µm. The Nd-YAG laser uses a solid crystal of yttrium aluminum garnet doped with neodymium and emits light at 1.06 µm, in the near infrared region of the spectrum. Excimer lasers use an inert gas halide as the lasing medium and emit light in the ultraviolet region of the spectrum; e.g. xenon fluoride produces laser light at 351-nm and argon fluoride laser light at 193 nm.
The CVL produces green and yellow laser light at 510 and 578 nm respectively.
Back to TopCopper Vapor Laser
As its name implies, the copper vapor laser uses vaporized copper atoms as the lasing medium. The laser head for a CVL is schematically shown in Figure 3.
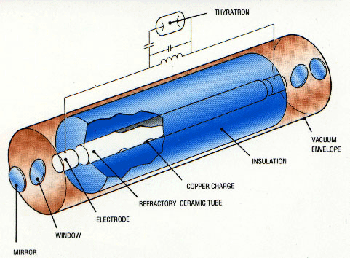
The refractory ceramic tube contains pellets of copper and a low-pressure buffer gas, usually neon. A pulsed electrical discharge between electrodes at each end of the tube raises the temperature to about 1450 C (2642 F), producing a copper vapor at a low partial pressure. Excited electrons in the electrical discharge collide with the vaporized copper atoms and excite them in a single step to the upper 2P3/2 and 2P1/2 laser levels illustrated in Figure 2. The electrons in the 2P3/2 level decay to the lower 2D5/2 laser level producing green laser light at a wavelength of 510 nm. Transitions from the 2P1/2 to the 2D3/2 level produce yellow laser light at a wavelength of 578 nm.
The CVL laser beam has many characteristics that are beneficial to precision micromachining. First, many materials efficiently absorb visible light, and, as it happens, the output power of copper vapor lasers is greater than that of other visible lasers. Next, electrons in the lower lasing level require a relatively long time to relax to the ground state, hence the population inversion cannot be sustained continuously and the laser action self-quenches. The power of the laser is therefore contained within very short 5-60 nanosecond pulses, each pulse having a very high peak power; typically 50-5000 kW. Finally, the lasing cycle has a very high repeat frequency, and pulse repetition frequencies of 2-100 kHz can be obtained. These pulse rates are higher than that of any other high-power visible laser. It is, in fact, the copper vapor laser's combination of high power and fast pulse repetition rate that enables it to attain high machining rates.
As additional benefits, the simplicity of the laser head gives the CVL a long operational lifetime and excellent power stability and beam quality, all features that facilitate precision during micromachining operations.
Back to TopKinetic Enhancement of the Copper Vapor Laser
Kinetic enhancement is achieved by adding a small quantity of a hydrogen halide, typically 1% hydrogen bromide, to the neon buffer gas. This addition speeds up essential chemical reactions involving copper atoms that underpin the lasing action, resulting in a marked increase of the laser's optical performance. A major advantage of this simple modification is that the improved performance is achieved without the need to re-engineer the laser. Kinetic enhancement improves the following properties of the CVL.
- Output power is increased by a factor of 2-3
This is illustrated in Figure 4, which shows how the power of CVLs has increased over time. The improved performance of a kinetically enhanced model, LM100X, is apparent when compared with its non-enhanced counterpart, LS2010.
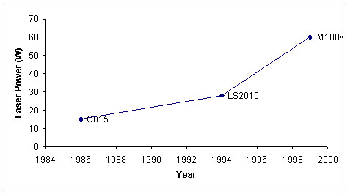
- Brightness is increased by up to 7 times
- Power is almost independent of pulse repetition frequency
This property is illustrated in Figure 5. Note that output power is almost flat from 10-40 kHz.
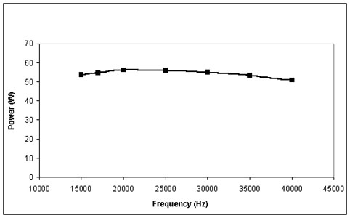
These benefits collectively reduce machining cost since the same performance can now be obtained from a smaller, less expensive machine or faster machining rates can be achieved with the higher available power. The higher brightness and faster pulse rate also further improves the micromachining capabilities of the CVL as will be explained in the next section.
Back to TopMicromachining with the Copper Vapor Laser
The copper vapor laser has several characteristics that make it the ideal machine for precision micromachining:
- Light of the CVL's wavelength is naturally absorbed by metals and hard materials to give highly efficient material removal at almost any angle of incidence.
- The CVL can machine metals, diamond, silica, glass, silicon, ceramics and many other materials that are difficult to machine by conventional techniques.
- The CVL excels at high-aspect-ratio drilling and slotting.
- The very high peak power density removes the material either by vaporization or ablation resulting in minimal dross, splatter or recast material thus giving clean and precise machined features that do not require finishing operations.
- The small amount of energy contained within the short pulses minimizes thermal effects.
- The high pulse rate gives high machining speeds.
- The excellent beam quality produces extremely small spots with very high power densities that can machine small features from 1 µm upwards.
- The stability of the pulse energy ensures that each pulse removes the same amount of material thus maintaining precise dimensional control.
- Frequency doubling of the CVL produces a similarly pulsed laser beam in the ultraviolet region of the spectrum, and this can be used for the precision micromachining of plastics.
The capabilities of the CVL are illustrated by the following examples.
Back to TopMicrodrilling
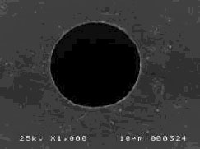
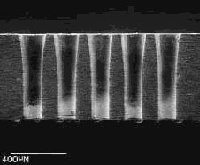
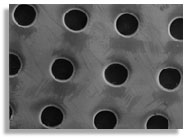
The CVL's microdrilling capability has already been illustrated with the 20-µm hole in a drill tip shown in Figure 1. This capability is currently exploited in the machining of holes in ink jet printer nozzles, an example of which is the 50-µm hole shown in Figure 6, as well as in fuel injectors for automobile engines.
The hole shown here is in the as-drilled condition. It is perfectly circular and its edges are sharp and burr-free, thus eliminating the need for post processing operations. The ability of the CVL to drill high aspect-ratio holes with a controlled taper is illustrated in Figure 7. Here, 130-µm holes flared at one end have been drilled in 600-µm thick alumina.
Figure 8, illustrates the machining of plastics, for which the frequency of the laser beam was doubled. Here, an array of 100-µm holes has been drilled in a plastic sheet. The edges of the machined holes are clean and burr-free and do not require any further processing.
Back to TopMicrocutting and Micromilling
The CVL laser's microcutting and micromilling capabilities are illustrated in Figure 9, which shows precise grooves cut into the surface of artificial diamond. Lubrication grooves can be cut into the surface of materials for aerospace and automotive applications, as in the piece of aluminum shown in Figure 10, in which 500-µm cubes are separated by 100-µm wide trenches.
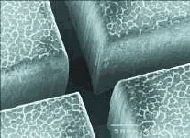
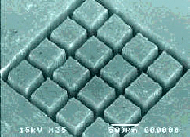
Artificial cracks with widths as narrow as 4-5 µm and extremely high aspect ratios can be produced in materials used for nondestructive testing. The picture shows a 60-µm wide, 3-µm deep artificial crack produced by CVL micromachining of a metal block.
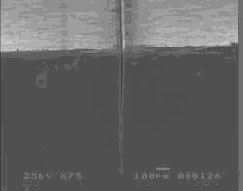
Other Applications of the Copper Vapor Laser
While the CVL is ideally suited to micromachining, it has a number of other uses. In fact, one of the first applications of the CVL was for atomic vapor laser isotope separation for the enrichment of uranium reactor fuel. The CVL is also used as a source of very intense stroboscopic lights for high-speed photo-graphy and flow visualization, e.g., illuminating the shock wave from a super-sonic projectile. The illustration in Figure 12, shows five frames from a high-speed film of diesel injection and combustion viewed through the piston of a research engine.
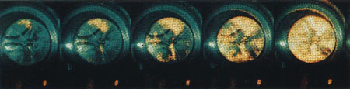
The CVL beam can also be used for holography, projection televisions and to observe events in intense emitters of light such as plasmas produced in welding and cutting torches.
Back to TopFuture Prospects for the Copper Vapor Laser
The CVL has a very promising future since the demand for micromachined components is accelerating year on year. The inherent characteristics of the CVL make it the natural choice for precision micromachining, and the reduced operating costs made possible by kinetic enhancement will inevitably expand the number of applications for this highly versatile laser.
Also in this Issue:
- Phosphor Bronze: Teaching an Old Dog New Tricks
- Copper at the Cutting Edge: The Copper Vapor Laser
- Maitreya Project: Nickel-Aluminum Bronze Selected for World's Largest Statue