New Life for Old Boards
Copper Applications in Health & Environment
A microchip from your old 1984 computer might be granted a new life in the next millennium, thanks to the joint efforts of Hewlett-Packard and Micro Metallics Corp. (Micromet), a San Jose-based computer recycling company and wholly-owned subsidiary of Noranda Inc. of Canada. The progeny of this union, launched in 1996, is one of the largest processors of electronics materials for metal recovery in the United States.
In a vast warehouse in the outskirts of Roseville, California, 180 employees of Micomet lead the industry in creating an afterlife for discarded computer products. This enterprise came into being with the formation of a strategic alliance between Hewlett-Packard's Hardware Recycling Organization (HRO) and Micromet back in 1996. The coalition was created to facilitate a way for HP to efficiently and conscientiously dispose of the thousands of pieces of hardware the company withdraws from its worldwide operations every month.
"With advancing technology, PCs become obsolete faster, their parts have less value, and the need for more recycling grows," says Steve Skurnac, president of Micromet.
To address this problem, Hewlett-Packard, a leading global manufacturer of computing, communications and measurement products, teamed with Micro Metallics, a subsidiary of Noranda, a diversified metals and mining company. Noranda Inc. has been recycling electronic, telecommunications and other equipment for almost 20 years. Discarded electronics and other recyclables are an abundant source of metals such as copper, silver, gold and platinum, and recovering them takes less energy (10 percent less for copper) while producing much less waste (potentially 98 percent less). But this is only part of the environmental and economic benefits of computer parts recycling. Salvaging computer parts can also:
- Reduce volumes of material that end up in landfill sites;
- Offer energy savings by reducing the need for mining and milling;
- Provide essential materials utilizing a relatively sulfur-free process; and
- Cause fewer environmental stresses, such as land disturbance and water discharges.
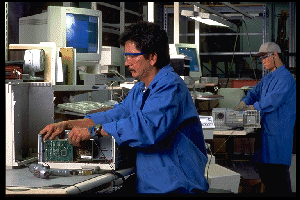
What exactly happens to an obsolete computer or computer peripheral once it arrives at Micromet? First of all, any part is removed that can be refurbished and used to repair other machines, or sold secondhand to parts dealers. Circuit boards with valuable parts, such as microprocessors or memory chips, are sent to a vendor elsewhere to be extracted. Other circuit boards with less valuable parts are shipped to another division of Micromet to be shredded and shipped to Noranda's copper smelter in Quebec, Canada, for metal recovery.
The remaining debris generally consists of plastic cases, copper from old motors or insulated wires, and steel or aluminum parts that have no value other than to be ground up and sold for scrap. That's when Micromet's $3.5 million machinery goes into action chewing up big chunks of equipment and spitting out small flakes of steel, aluminum, copper and plastic. Two runs are then made over this scrap to cut it down to smaller and smaller shards, ultimately leaving pieces about the size of a quarter.
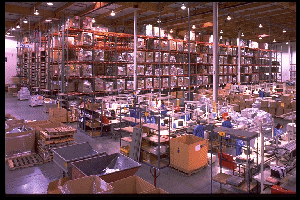
The copper, which has been shredded, falls through a 15-millimeter screen to be shipped off to Noranda's smelter. Noranda's facility also deals with pieces that don't get the crunching treatment. Computer monitors are received intact at Noranda and melted down to extract coils of copper. If this Canadian recycling facility were classified as a mine, it would account for 5 percent of the copper, 5 percent of the gold, 14 percent of the silver, and 37 percent of the platinum group metals mined in Canada. Recyclables can contain ten times more copper and 50 times more gold than average mined ores.
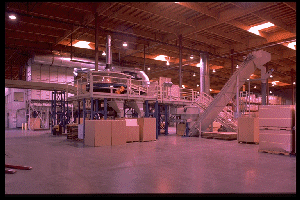
"Nothing goes into the landfill," says Skurnac.
HP and Micromet have a synchronous arrangement, with Micromet employees doing all the disassembly and recycling, HP marketing the usable parts that are removed early in the process, and Micromet, finally, either selling the scraps directly, or shipping the scraps to Noranda smelters. Monies made from these undertakings are kept within their family of companies.
The new metal-separation program, begun in 1997, can handle more business than even HP can provide. Renee St. Denis, HP's end-of-life process manager, says that so far her company is just breaking even on the arrangement. Right now, Micromet processes up to 3 million pounds of PCs, printers and other high-tech equipment every month and has capacity to do more. As more and more computers are being replaced as technology progresses, Micromet and HP are prepared to handle the obsolete equipment in an environmentally sound manner.
Also in this Issue:
- New Life for Old Boards
- Copper Busbar Sizing Guide
- New Copper Alloys - Winter 1998 Notes from CDA's Technical Service Advisory Committee December, 1998 Meeting