Introduction to Copper: Applications
Copper Applications in Metallurgy of Copper & Copper Alloys
Introduction | General | Electrical | Commercial/Industrial | Building Construction | Architecture | Industrial
Introduction 
This article is intended as an introduction to copper, describing the many ways in which the metal is so useful. The article also touches on copper's invaluable contribution to the health of plants, animals and mankind. The article is not meant to provide a comprehensive compilation of data for use in selecting copper for particular applications; plentiful information of this type can be found on The Copper Page and in other references cited in the following text. Rather, it provides an overview of copper and its properties and a guide to lead the reader to appropriate sources of data.
Each one of the topics mentioned in the list of contents could justify not only another article; in fact, most of these topics have been the subject of complete books giving much more detail. At the end of the article is a list of links that will get you to Web sites with more information. Other links and references are cited within the text. These citations cover most of the topics mentioned in the article. There is also a link to the Copper Data Center, CDA's large bibliographic database of useful published books and articles.
General 
Copper and its alloys possess a very wide range of properties that make them invaluable for many applications. Each of the thousands of uses employs a combination of these properties to help ensure material that is ideally suited for the purpose. Good conductivity of electricity and heat is combined with strength, ductility and excellent corrosion resistance, to mention just a few of the properties that copper and its alloys offer.
Table 1 lists some of the reasons why copper and copper alloys are vital to the major types of application that benefit from combinations of the attributes described.
Property | Industry/Type of Application |
---|---|
Aesthetics | Architecture, sculpture, jewelry, clocks, cutlery. |
Bactericide | Door hardware, marine internal combustion engines, crop treatments. |
Biofouling resistance | General, hydraulic and marine engineering, metalworking, aerospace, power generation, shipbuilding, offshore oil and gas platforms. |
Corrosion resistance | Plumbing tubes and fittings, roofing, general and marine engineering, shipbuilding; chemical engineering, industrial processes including pickling, etching and distilling; domestic plumbing, architecture, desalination, textiles, papermaking. |
Ease of fabrication | All of the above plus printing. |
Electrical conductivity | Electrical power generation, transmission and distribution, communications, resistance welding, electronics. |
Environmental friendliness | Essential for health of humans, animals and crops |
Fungicide | Agriculture, preservation of food and wood. |
Low temperature properties |
Cryogenics, liquid gas handling, superconductors. |
Mechanical strength/ductility |
General engineering, marine engineering, defense, aerospace. |
Non-magnetic | Instrumentation, geological survey equipment, minesweepers, offshore drilling. |
Non-sparking | Mining and other safety tools, oxygen distribution. |
Elasticity | Electrical springs and contacts, safety pins, instrument bellows, electronic packaging. |
Thermal conductivity | Heat exchangers and air-conditioning/refrigeration equipment, automotive radiators, internal combustion engines, mining. |
Figure 1 illustrates the main reasons for using copper. The figure is based on results of a survey of the primary properties required when copper is being selected for the manufacture of products.
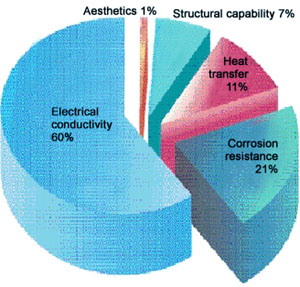
Remember, though, that besides the principal property, it is always a combination of properties that are important for selection of the most suitable, cost-effective, material in every application.
Copper has made possible the continued, efficient development of the electrical industry because it has the highest conductivity of the commercial metals. In addition, it has favorable mechanical properties at low, ambient and elevated temperatures, is easily fabricated or cast to shape and can be readily machined. Copper also has excellent resistance to oxidation and corrosion. The thin oxide layer that does form is conductive; meaning that properly made connections will have a long service life and will not deteriorate over time. From high voltage transmission cables to microcircuits, and from megawatt generators to computers, in every aspect of electrical generation, transmission and use, copper is the essential, energy-efficient metal.
Modern electronic and computer technology has created requirements to meet extremes of service conditions that demand very special materials. For example, tensile strengths greater than 200 ksi (1400 MPa) can be achieved in heat-treatable alloys such as beryllium coppers; therefore such materials are often selected for heavy-duty industrial and military electrical connectors.
Copper's high electrical conductivity is matched by excellent thermal conductivity, which makes copper the first choice for heat exchanger applications. Good examples are the recently developed brazed copper-brass automobile radiators that are fully competitive with aluminum counterparts in terms of thermal efficiency and light weight, and are significantly more durable.
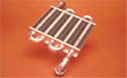
Figure 2. Heat Exchanger Matrix
This oil cooler is designed to be cheap to make and efficient in use. Copper tubes are inserted in a stack of pierced copper fins and hot dip soldered to make a strong matrix with corrosion-free long service life. (ICA).
Copper and its alloys represent 6 - 9% by weight (or approximately 50 - 55 lb, 23-25 kg) of the content of a typical automobile. Copper itself is essential for the full wiring harness, alternator and starter motor windings and other motors and actuators. Copper alloys are used for conductive spring clips, terminals and connectors. Copper alloys are also used for bearings, gears and valve guides, radiators, hydraulic tubing, and fasteners. Small, machined components can be made cheaper in brass than in steel, and, for automotive applications, generally do not need expensive protection against corrosion. Copper is also an essential component of aluminum alloys used for engine blocks, cylinder heads and other automotive castings. And, copper is beginning to play an important role in electric and hybrid vehicles, in starter motor/generators, drive motors, circuitry and as the cathode in recently commercialized nickel-metal hydride batteries. In all, the copper content of future vehicles may be three times that used today.
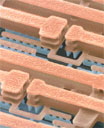
Coppers and copper alloys exist that meet almost any foreseeable industrial need ranging from miniaturized components of modern electronics to multi-ton products for heavy industry. Common engineering applications include valves, pumps, heat exchangers, vessels, brakes for large aircraft and off-road vehicles, sleeve bearings for innumerable mechanical products, ship propellers and plastic injection molding dies. Copper's use in our homes and industries generates no risk to health; indeed, copper is an essential trace element in our diets.
Recent developments in semi-conductor technology have included the use of copper to help boost performance by 30% and reduce size. 200 million transistors can be packed into a single chip. (IBM)
Despite its widespread (and growing) usage, there is no risk that natural resources will become depleted. Copper is mined in many places throughout the world, and new metal is usually in plentiful supply. On the other hand, copper also has the enormous advantage of being readily recycled. It is easily separated from other scrap and can be reused economically. Indeed, copper's high recyclablility has been cited as one of the metal's "green" properties.
Table 2 lists materials-selection factors that arise with alternatives to copper, but that need not be considered when coppers and copper alloys are selected:
Factor | Effects |
---|---|
Rusting | Corrosion of steel is a continuous process giving a large volume of rust that flakes off. This is particularly detrimental under electroplating or when steel is embedded in concrete. |
Degradation by sunlight or ultra-violet (UV) radiation | Many plastics suffer from this phenomenon, which results in loss of properties and degraded appearance. |
Attack by ozone | Rubbers and plastics degrade; embrittlement effects similar to UV attack. |
Migration of plasticizer | Many plastics suffer this problem, which leads to embrittlement and loss of strength. |
Loss of properties at slightly elevated temperatures | Many plastics lose strength rapidly above ambient temperatures. |
Low-temperature embrittlement | Many metals and most plastics become brittle at low temperatures. |
Rapid formation of a non-electrically conducting oxide layer | Aluminum develops an insulating oxide film that can produce arcing in electrical connections. |
Requirement for expensive molding tools | Production processes for many plastics are expensive to set up. |
Material | Testing Temperature | Min Creep Rate | Stress | ||
---|---|---|---|---|---|
°C | °F | %/1,000h | N/mm2 | KIPS | |
Al | 20 | 68 | 0.022 | 26.0 | 3.7 |
Cu-ETP | 150 | 302 | 0.022 | 26.0 | 3.7 |
Cu-0.086% silver |
130 | 266 | 0.004 | 138.0 | 20.0 |
Cu-0.086% silver |
225 | 437 | 0.029 | 96.5 | 13.9 |
Electrical 
The vast majority of electrical applications call for the use of conventional high-conductivity copper, and these applications account for the more than 60% of all newly refined copper produced. Unless otherwise identified, it is this type of copper that is most often referred to in the descriptions of applications that follow.
Copper Cabling
Copper has higher electrical conductivity than all metals except silver. It is for this reason that it is used in commercial and domestic buildings to provide the energy-efficient, safe, electrical distribution systems upon which we all rely. Copper wire is strong enough for the purpose, yet fully ductile when bending is needed. It does not react with modern insulation materials. It retains a low contact resistance throughout its long life, even when tarnished, and connections remain safe. Copper also has relatively high creep strength, meaning that connections made in screwed terminals do not relax over time, or when the operating temperature is reached.
Domestic Uses
The amount of high conductivity copper used in domestic buildings has increased steadily to keep up with the demands posed by the growing number of electrical and electronic appliances in use. Older buildings, and even some new ones, are often not fitted with enough branch circuits, let alone outlets, to cope with this high demand.
Commercial/Industrial 
The continuous availability of a high quality electrical power supply is essential to the economy of a business. Power failures can mean loss of data and customer confidence. When electrical installations are being designed, either for new buildings or to upgrade existing buildings, it is vital that power quality, reliability, resilience, energy efficiency, proper grounding (earthing) and future load growth are taken into consideration.
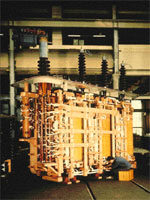
Energy Efficiency
This is the interior of an oil-filled transformer showing high conductivity copper windings that are ductile enough to be formed accurately to shape yet strong enough to take the very high electromagnetic stresses that develop during a short circuit.
By selecting energy-efficient motors and larger sized copper conductors for industrial applications or heating and ventilation systems in commercial buildings, considerable savings in running costs can be made with relatively short payback periods. The reduction in power consumed by energy-efficient installations including transformers, cables, bus bars and motors, leads to cost savings to users and reduced emissions to the environment from power stations. In fact, higher electrical efficiency brought about by more extensive use of copper, when broadly applied, reduces the need for additional generating capacity. See Energy section for further information on copper's energy-saving qualities.
Power Quality
Modern electronic loads, such as motor controllers, and the switched mode power supplies used by personal computers, draw high levels of harmonic currents that do not cancel in the neutral of a three-phase system. The common practice of using half-sized neutrals is unsound wherever harmonics are likely to be present, which nowadays means almost every commercial and industrial installation, and the use of double-sized neutrals is now a recommended practice. (See Power Quality section for several informative articles on this subject.) One easy solution is to use five-core copper power cable - three cores for the phases and two for the neutral. Integrating the fifth core with the cable ensures good current sharing between the neutral cores.
Grounding (Earthing)
Where earthing must have low impedance, there is a strong case for adding an extra copper conductor rather than relying on unreliable joints in steel armoring and conduit. In fact, the Institute of Electrical and Electronic Engineers (IEEE) has for many years made installation of a "green wire" grounding conductor one of their recommended practices. Power supplies for computers and the electronic controls for most modern equipment rely on an earth leakage current to stabilize the voltage. Any breakage of earthing circuits will now result in dangerous voltages and must therefore be avoided at all costs.
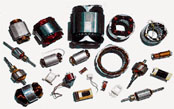
Electrical Engineering
These are wound with copper wire coated with a thin layer of insulating, heat resistant enamel. The high quality copper used ensures that the coils wind easily and give a reliable, energy-efficient lifetime of service.
High conductivity copper is used for electrical windings of all types of equipment to ensure reliability, compactness and energy efficiency. Here, it's truly a case of "the more copper, the better". For example, a U.S. law known as the Energy Policy Act of 1992 (commonly called EPAct) mandates that electric motors of certain types sold after 1997 must meet specified levels of electrical energy efficiency. The efficiencies of the listed motors are, generally speaking, between one and four percentage points higher than those of older, conventional motors. (In the years since implementation of EPAct, so-called "Premium Efficiency" motors have been developed that are even more efficient than those covered by the 1992 law.) All of these improved motors owe their higher efficiencies in large part to the fact that their windings contain approximately 20% more copper than their predecessors. Incidentally, one to four percent may not sound like much of an improvement, but it's sufficient to yield savings of tens of thousands of dollars in an industrial motor over its lifetime � many times the cost of the motor itself.
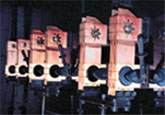
These busbars are typical of many used in industrial environments to carry heavy currents for many years without the need for significant maintenance. The high conductivity copper is energy efficient and the joints remain low-resistance. (Thomas Bolton).
Pure copper is a moderately strong metal, but there are many applications that require high conductivity along with high strength, high hardness or wear resistance. For such applications, designers select from a family of what are called "high copper alloys" in the U.S. and "high-strength high conductivity alloys" in some other countries. They contain small amounts of potent strengthening elements such as chromium, zirconium and beryllium, among others. Typical applications for such specialized alloys include electrical contacts and switches, catenary wire (also called trolley wire) electric railroads, resistance welding electrodes, motor end rings and computer components.
Building Construction 
Plumbing
The ancient Egyptians were probably the first to use copper tubes to deliver water where it was needed. Since then, copper has become widely adopted as a safe, economic material for water services. In the USA., about 80% of all plumbing tube is copper; in the U.K., the figure approaches 100%. Plumbing tube and fittings comprise the second-largest use of copper, after electrical applications.
Copper tubing is light and strong enough for the pressures involved and other stresses in the installations. It is easy to cut, bend and join and can therefore be installed quickly and reliably, usually outlasting the building it serves. It inhibits the growth of many microorganisms and has been shown to be the most hygienic material for potable water supplies. It is unaffected by hot water and this fact, plus copper's high thermal conductivity, makes it ideally suited for use in central heating systems. Plumbing tube can be made from newly mined and refined copper, but it is more often made from remelted and suitably re-refined scrap copper. In the USA, about 65% of plumbing tube is made from copper that had been used before (see Good for Consumers, Good for the Environment). The amount of scrap used in any given plant depends on a number of factors including the type of melting equipment at hand, availability and the cost of transportation for either commodity, and the price difference between new copper and scrap. Whatever the raw material, plumbing tube is generally produced from copper that has been deoxidized with phosphorus, the most common grade being UNS C12200.
Architecture 
Roofing
Copper has been used as a roofing material from at least as early as 27 BC. When the Pantheon in Rome was built it was roofed with copper, as were several early Japanese shrines. The suitability of the metal as a roofing material has been further proved over the succeeding centuries. The essential attributes of good long-life roofing material include an attractive appearance, high corrosion resistance, minimum maintenance requirement and good economy. Copper combines all of these qualities better than any other weathering material and is therefore an excellent choice for a roof covering. Taking first cost and maintenance costs over the first fifty-year period of a roof, copper is amongst the cheapest materials to use. There have been concerns expressed over the potential toxicity of copper-containing runoff water from roofs, an issue raised in some European countries and in the State of Connecticut, among other places, but recent research (see New Research on Runoff from Copper Roofs) shows that complexing by natural organic matter and combination with water-borne ions renders such copper "totally inactive — or not bioavailable" (in the words of the report) a few hundred yards from its site of origin.
Other Applications
Copper and copper alloys are used for many other applications such as wall cladding, frames for doors and windows, structural fixings and decorative trim to name but a few.
Industrial 
For many years, copper has been used in industry. Besides being essential in all electrical installations, typical applications are for the manufacture of pressure vessels, distillation equipment, piping systems and gaskets.
Also in this Issue:
- Introduction to Copper: Applications
- Introduction to Copper: Types of Copper
- Introduction to Copper: Mining & Extraction
- Introduction to Copper: Fact Sheets
- Phelps Dodge Morenci Has Converted All Copper Production to Mine-for-Leach
- How Hydrometallurgy and the SX/EW Process Made Copper the "Green" Metal
- Introduction to Copper: Hot Links & Further Reading